The Cultured Coconut Case Study
“..they were, from a personality or meshing perspective, great to work with. They did due diligence. I mean they walked around our facility and catalogued things really well for us and set us up for future work.”
Linda Peers
Founder, The Cultured Coconut
About the Client
Cultured Coconut
The Cultured Coconut, founded by Linda Peers in 2015, offers a unique dairy-free probiotic drink made from fermented coconut milk. This product contains over 4 trillion CFU of live probiotics per tablespoon, promoting gut health.
Initially launched in Nova Scotia, it has expanded to various Canadian retailers due to high demand and positive customer feedback and is currently making massive strides into the US market.
Understanding the Problem
The Challenge
As the business organically outgrew its humble beginnings, orders began to rush in. This challenge of scale meant that quality had to be rigorously monitored. A slight deviation of 5-degrees Celsius could ruin a batch of product, impede productivity, and result in costly waste and unfulfilled orders.
The Cultured Coconut Team
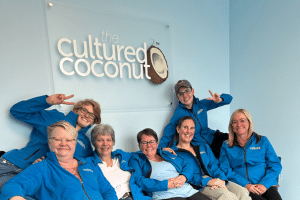

Production worker standing proudly in front of bottling machine
Bottled production ready for distribution
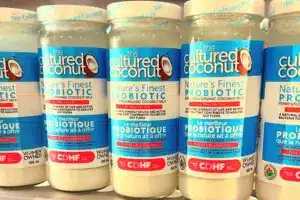
Solving the Challenge
The Solution
To minimize production risks, Enginuity designed a straightforward temperature alerting system. Sensors were placed inside fermenting tanks and connected to Opto 22’s groov RIO platform, which uses programmable logic to automatically email staff if temperatures move outside a defined threshold.
This system represented a low-cost, high-impact quality control automation solution that addressed immediate needs while laying a foundation for future process improvement. Enginuity selected groov RIO based on its flexibility, scalability, and prior successful use in food and beverage automation.
Summarizing the Outcome
The Conclusion
It’s a misconception that improving production effectiveness requires a massive overhaul. With the strategic addition of temperature sensors and an integrated notification system, The Cultured Coconut now operates with reduced risk of costly failure.
This enhancement allows the team to maintain high product standards while confidently scaling to meet growing demand, both in Canada and abroad, with smarter, more reliable food production automation.
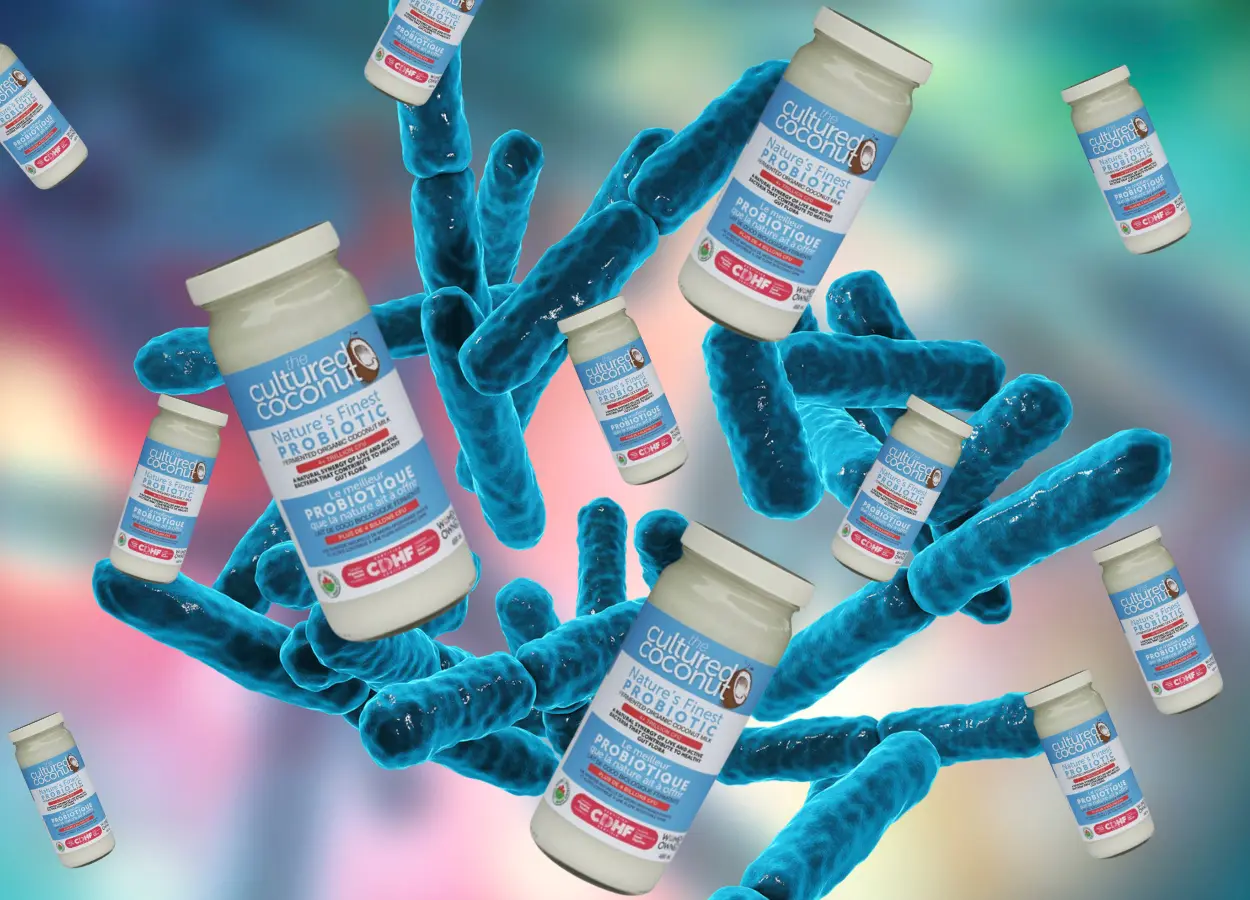
Read the Impact
Healthy Business, Healthy Belly
Key Takeaways
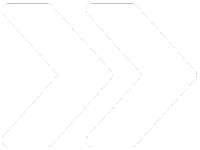
Process Optimization
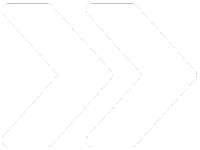
Remote Monitoring
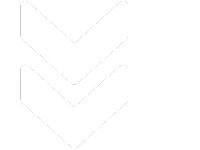
Cost Efficiency
Read Other Success Stories
See How We Are Shaping The World
Product Development
Everything you need to get your product development done quickly, creatively, and on budget.
Industry 4.0 & Robotics
Integrating traditional manufacturing and industrial platforms and practices with the latest smart technology.
Aerospace & Defence
Providing safe, controlled and reliable engineering for Aerospace and Defence projects.
Industrial & Marine
Helping you develop reliable engineering solutions for harsh environment offshore operations.