Doubling Production with Food Packaging and Production Automation
Enginuity transformed our complex, fragmented facility into a streamlined, automated operation. They addressed our building’s unique challenges, integrating automation to move cans efficiently over large distances. We couldn’t have achieved this without their expertise in production and packaging automation.
Phil Leblanc
Owner, IMO Foods Ltd
About the Client
IMO Food Ltd.
Understanding the Problem
The Challenge
The company has been looking into increasing automation for their food manufacturing facility because they needed to stay competitive in the food industry and meet market demands from grocery leaders, all while struggling with an ongoing labor shortage in rural Nova Scotia. Furthermore, with a constrained supply chain in the food and beverage industry due to the ongoing COVID-19 pandemic, the demand for their product increased further.
Like many food processing plants that have operated for many years, inefficiencies existed in their process, particularly in packaging automation to meet specific client orders. The incumbent process had several separate, manual steps that had the potential to cause bottlenecks, reducing production output.
Site Layout Inspection & Planning
We started with initial site inspection and planning to find scopes of production optimization consideration of building envelope limitations.
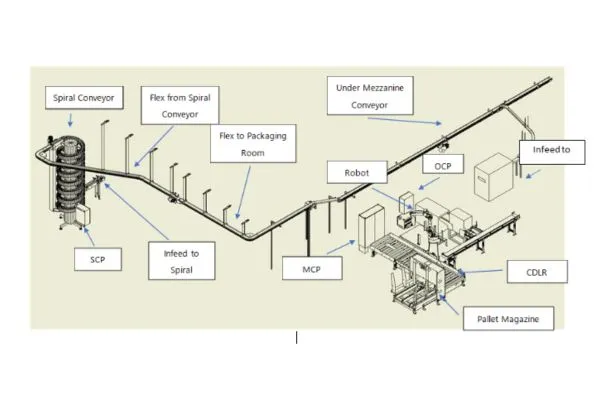
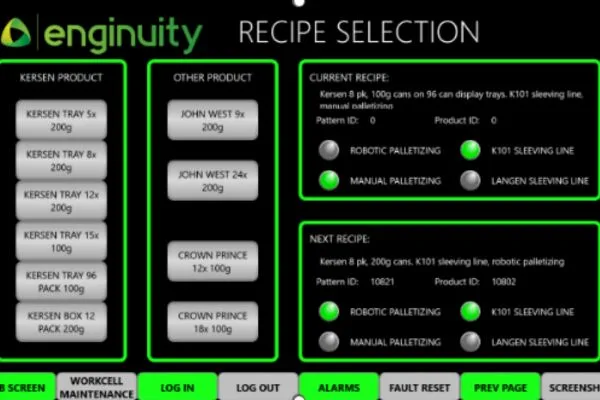
Production Facility
Palletizing robot in action.
Prototype Site Tour
Owner Phil Leblanc giving Enginuity Team and other industry leaders tour of the new packaging line.
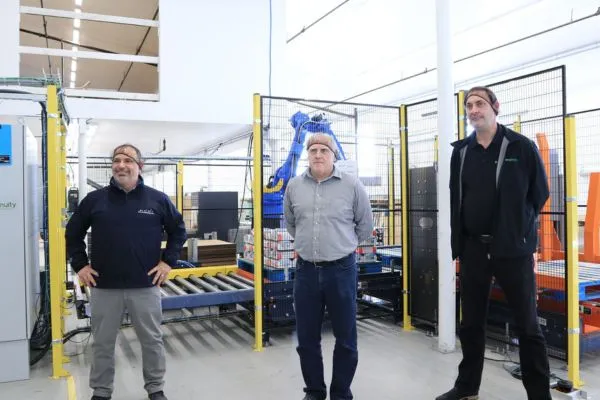

Creating SCADA solution
We built in a SCADA (Supervisory Control and Data Acquisition) solution that offers insight and added functionality into the entire process, offering a visual snapshot of the production system.
Fish Can at Costco
Herring and Sardines fish can at Costco. The Robotic palletizing allows for customized stacking patterns for each product

Solving the Challenge
The Solution
Following an Automation Study, IMO Foods engaged Enginuity for a process walk-through. Using our Automation Control Process team, we developed a Preliminary Design and conducted a Test Install of conveyors and a packaging robot at our Halifax facility before implementing it in Yarmouth, ensuring no production downtime.
Enginuity eliminated most manual packing, reducing double handling and ensuring a systematic, automated process that increased food safety. The custom system addressed the physical limitations of the facility and marked the first step in fully automating the food packaging process. Cans are delivered via a 20′ spiral conveyor for final inspection, then packaged and picked up by a 6-axis Yaskawa robot for pallet stacking.
As part of the implementation, we integrated a SCADA solution offering insights and added functionality. The system, accessible from anywhere, also enables remote control and diagnostics, reducing operational costs. The SCADA system we implemented resulted in:
- Production forecasting
- Quality control analysis
- Machine health and maintenance requirements
- Batch, lot, and work order reporting
The Food industry automation solution we implemented ensured consistent quality control and faster response times to market demands. The comprehensive Food automation process control provided real-time insights and management capabilities, enhancing overall productivity.
Summarizing the Outcome
The Conclusion
Key Takeaways
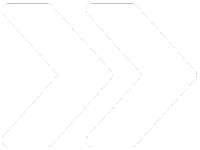
Optimized Production Process
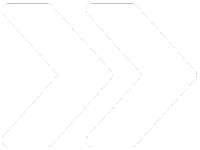
Significant Production Increase
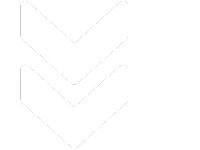
Positive Client Experience
IMO Foods saw high ROI potential and praised Enginuity for effective cost analysis and practical solutions.
Read Other Success Stories
See How We Are Shaping The World
Product Development
Everything you need to get your product development done quickly, creatively, and on budget.
Industry 4.0 & Robotics
Integrating traditional manufacturing and industrial platforms and practices with the latest smart technology.
Aerospace & Defence
Providing safe, controlled and reliable engineering for Aerospace and Defence projects.
Industrial & Marine
Helping you develop reliable engineering solutions for harsh environment offshore operations.