Scale Production and Optimize Performance
Turnkey PLC Based Solutions
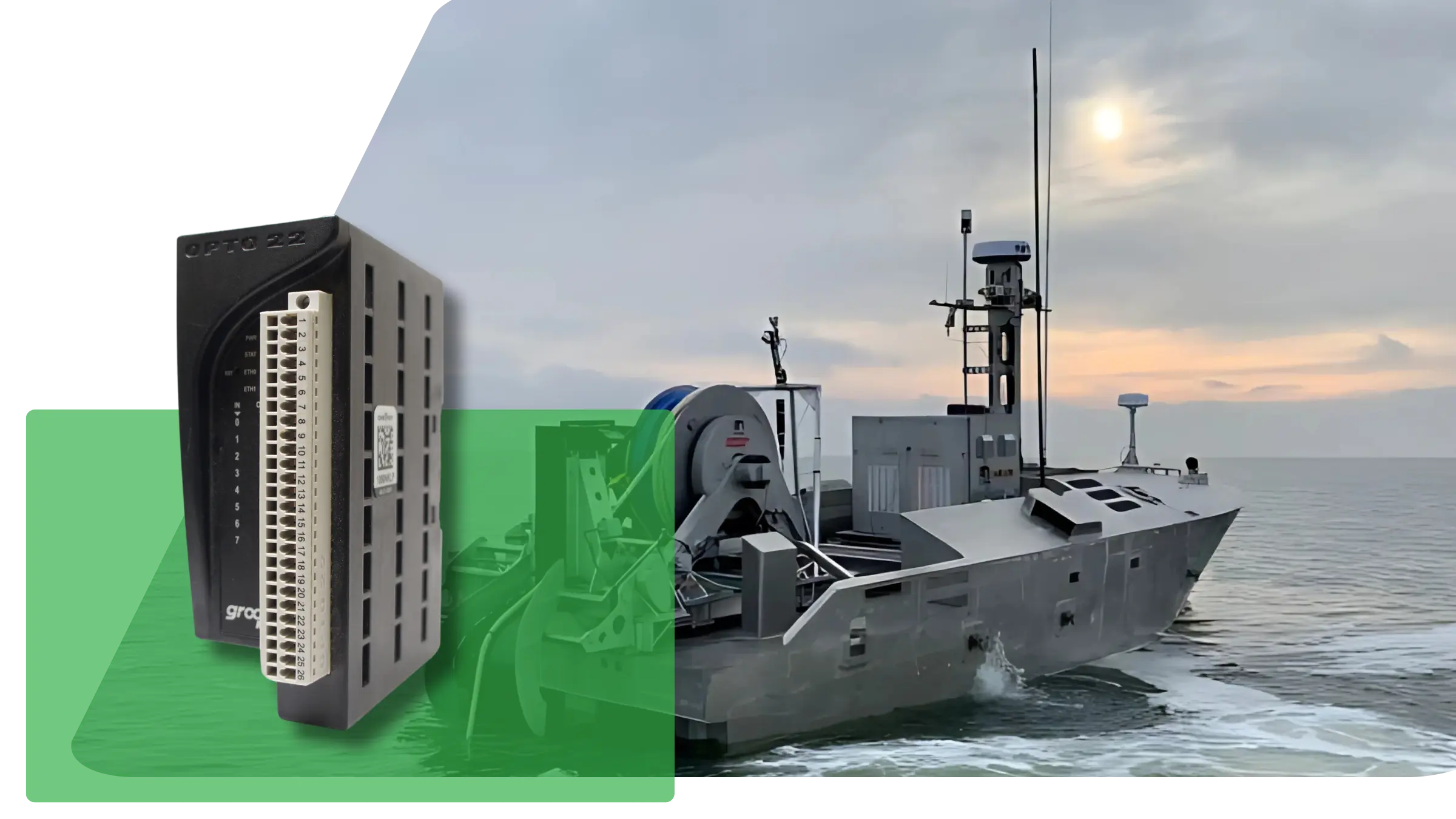
Break Free from Automation Limitations
Antiquated systems hold you back with inefficiencies and limited scalability. Upgrade with PLCs for flexible programming, instant troubleshooting, and seamless integration—your factory’s next step to smarter automation.
01
Programmable Flexibility
02
Real-Time Monitoring
Traditional systems lack visibility. We implement sensors that track temperature and pressure.
03
Streamlined Troubleshooting
Unclear errors cause delays. Our solution pinpoint issues instantly, cutting downtime and repair costs.
04
Scalable Solutions
Dated systems struggle to grow. Our systems scale with your production through reprogramming.
05
Seamless Integration
Multiple systems are tough to control. We centralize SCADA, HMI, and more for unified, remote control.
The Backbone of Intelligent Automation
We go beyond simple automation. To unlock their full potential, you need expertise like ours—a team ready to design, integrate, and reimagine your plant for the future.
Programming for Any Task
From simple tasks to highly complex processes, PLCs support a range of programming languages for your needs:
- Ladder Logic: Mimics traditional relay control for ease of use.
- Structured Text: Simplifies complex algorithms with a high-level approach.
- Function Block Diagrams: Speeds up implementation with graphical logic.
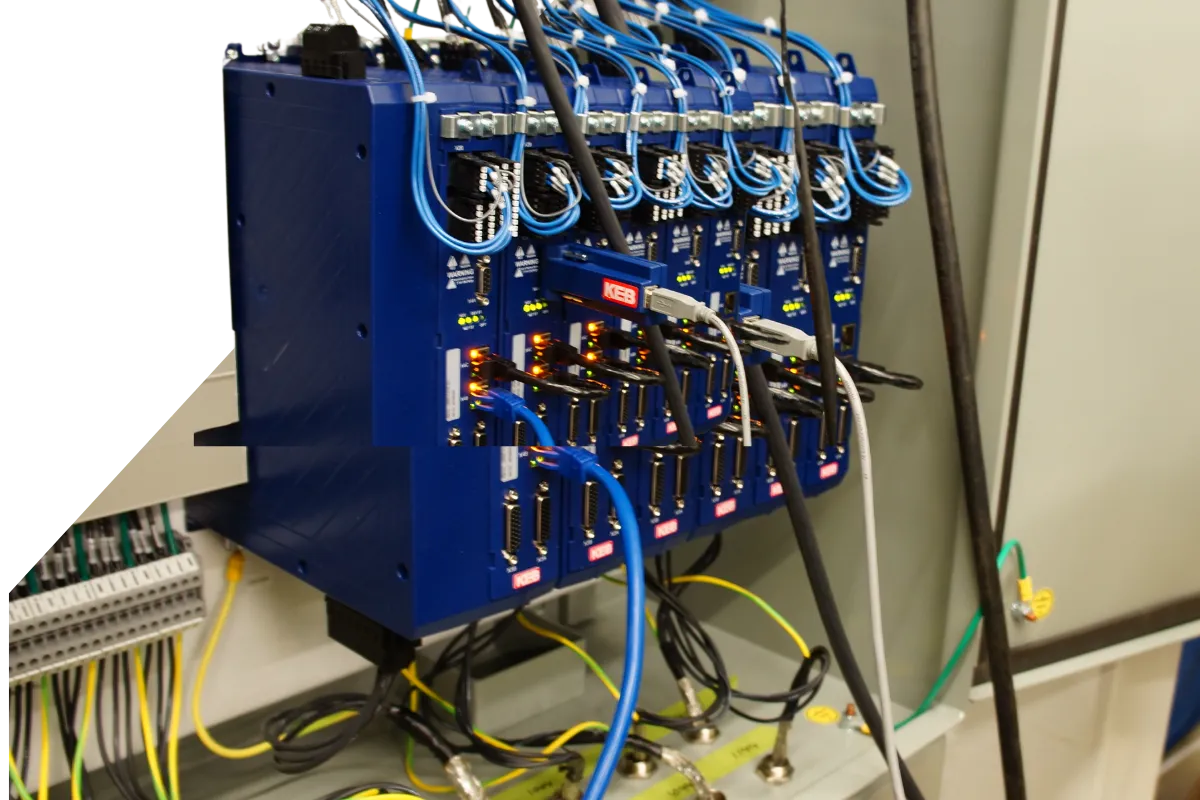
Act Before It’s Too Late
Get real-time visibility into equipment performance metrics like temperature, flow, and speed.
- Identify trends and address inefficiencies instantly.
- Optimize equipment lifespan with proactive adjustments.
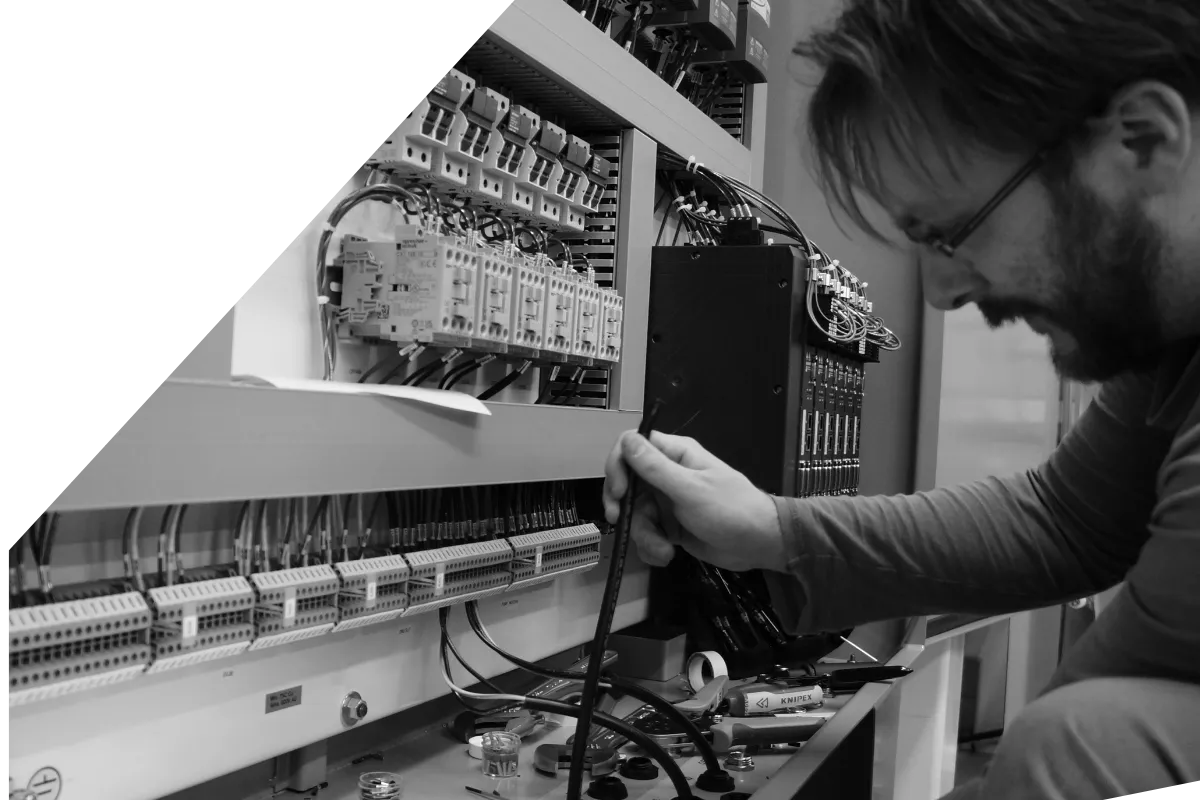
The Bridge to Industry 4.0
Modern PLCs connect machines, sensors, and systems into one unified ecosystem.
- Connect machines, sensors, and SCADA into one centralized ecosystem.
- Gain actionable insights with edge computing.
- Use advanced protocols like EtherNet/IP and Modbus TCP for flawless communication.

Built to Scale with Your Business
As your operations grow, PLCs adapt seamlessly:
- Add new processes or equipment with reprogrammable flexibility.
- Expand without replacing existing infrastructure.
A packaging facility scales from manual sorting to fully automated assembly lines without system rewiring.
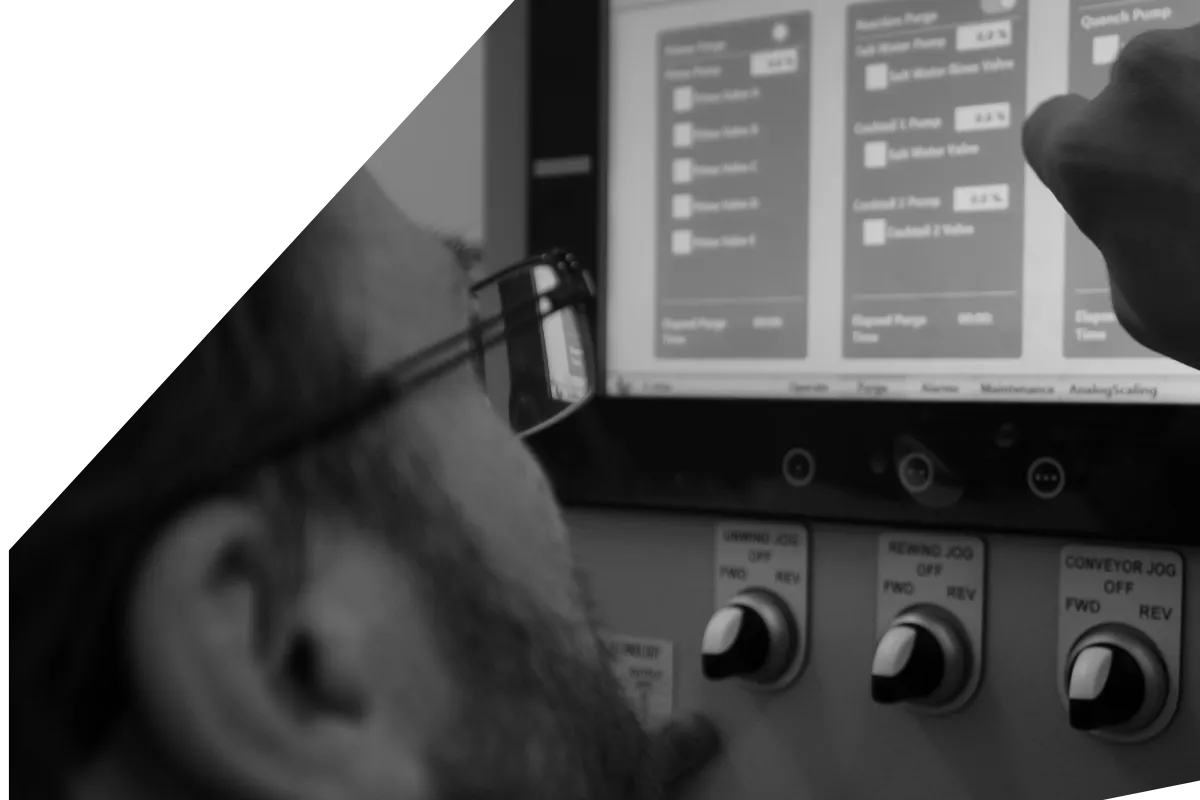
Key Clients




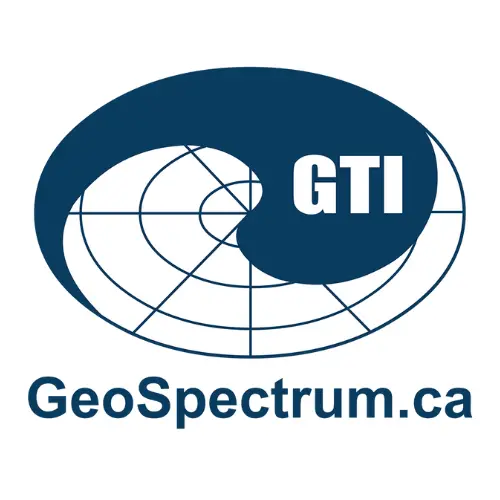


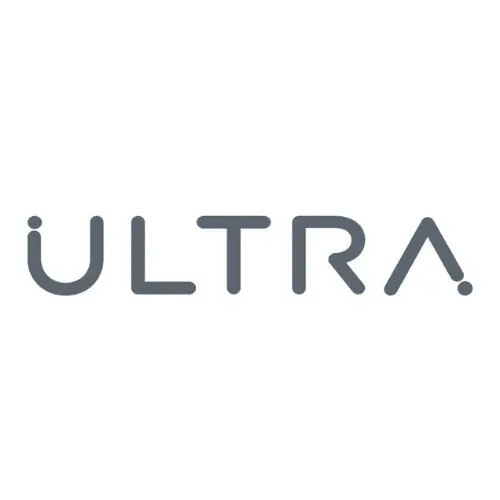



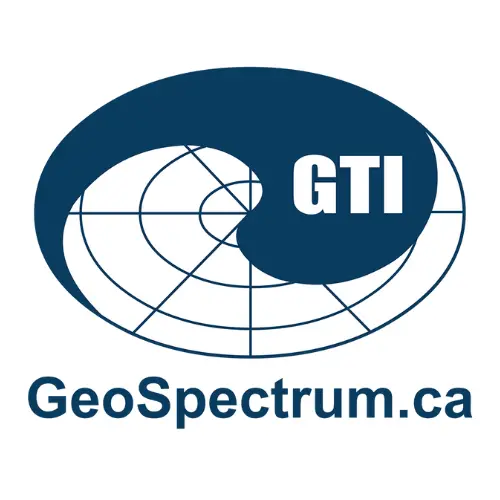
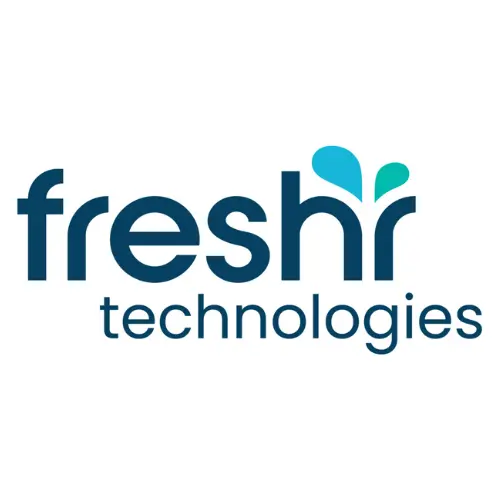
Case Study & Insights
case study
How Surrette Batteries Unlocked Efficiency Through Our Manufacturing Consulting Services
Frequently Asked Questions
Can PLCs Enhance Safety?
Yes, modern PLCs enhance safety with features like emergency shutdowns, fault detection, and safety interlocks. We ensure compliance with IEC 61508 and ISO 13849 for optimal safety.
Can you integrate PLC systems with IT/OT infrastructure for better visibility?
Yes, we integrate PLC systems with MES and ERP platforms to enable real-time data exchange, streamline production, and improve supply chain visibility.
By leveraging digital twins, IoT sensors, and PLC-to-enterprise connections, we ensure seamless operational data flow across facilities so plant managers feel empowered.
Do you have experience in robotics and motion control?
Can you integrate PLC systems with IT/OT infrastructure for better visibility?
How do you secure PLC systems against cyber threats?
We analyze your plant's vulnerabilities and network integrity to identify risks and implement tailored solutions such as OPC UA encryption, secure configurations, and firewalls. This protects your systems from cyber threats, ensuring your infrastructure remains secure and operations run smoothly.
How can edge computing in PLCs benefit my facility?
Edge computing in PLCs enables local data processing, reducing latency and reliance on external systems. This supports faster decision-making, real-time monitoring, and predictive maintenance, particularly in remote facilities or time-critical operations. Our solutions provide operations teams with actionable insights for production optimization.
Can your team integrate PLCs with legacy and modern equipment?
Which PLC platforms does your team specialize in?
What training do you offer to ensure our team can operate and maintain the system?
We offer customized PLC training programs tailored to your team’s needs. Training can be conducted on-site or online, covering key aspects like system operation, troubleshooting, routine maintenance, and advanced programming. Our sessions are designed for all skill levels, ensuring that every team member becomes confident and capable with the new PLC systems.
Additionally, we provide detailed operation manuals and refresher courses to keep your team up to date as your systems evolve, ensuring smooth and efficient plant operations over time.