Overall Equipment Effectiveness is becoming increasingly important as the world moves into Industry 4.0.
We’ll cover what OEE is, why it’s important, and how to calculate it with your own processes.
Overall Equipment Effectiveness is like a report card for your machine or automation process in the industrial Automation and Industry 4.0 world. It’s how Process Engineers, Plant Managers and Continuous Improvement Engineers measure how well their automation or process is working.
OEE is an extremely useful calculation/tool used to gain a complete and accurate picture of a machine or process that is often forgotten about. Instead of focusing on any one element in isolation, it instead multiplies 3 key calculations of equal weight to offer a key performance indicator (KPI) that holds far more value than any one metric analysed in isolation.
What key factors influence OEE?
These 3 calculations, availability, performance, and quality, are key to measuring overall performance in your automations and processes..
Availability in OEE
Availability in this context refers to the percentage of time that a machine, such as a conveyor belt, is able to operate during a shift or period of time. It is calculated by dividing the amount of time that the machine is running by the total amount of time in the shift or period, and expressing it as a percentage. This can be done by measuring the electrical current to the motor of the machine, and using a programmable logic controller (PLC) or computer to perform the calculation.
- If a machine conveyor belt is always running when the process is running, you could measure the electrical current to the motor to know when it is running
- Using a basic program in a PLC (Programmable Logic Controller) or computer you can then take that time and divide it by the total time over a shift (this is also equal to time on + time off). This basic calculation gives you availability
Performance in OEE
Performance is typically measured by comparing the actual output of the automation or industrial system (e.g. the number of cookies produced per minute) to the theoretical maximum output provided by the manufacturer. This comparison can be done by using a vision system or sensor to measure the number of cookies leaving the system, and then using a programmable logic controller (PLC) or similar device to perform the necessary calculations. The result is often expressed as a percentage, indicating how close the actual output is to the theoretical maximum. This is made easier with Industry 4.0 tech but it certainly isn’t limited to new technology.
- Get the speed by measuring the number of items/products or cookies leaving the system.
- Find the output rate by performing the necessary calculations, say, cookies per minute.
- Compare this number to the theoretical output of the system, perhaps from the manufacturer of the system.
- Comparing actual output rate to theoretical output rate would give you a metric expressed as a percentage that would act as your performance measurement.
Quality in OEE
Quality refers to the degree of excellence or merit of a product,use a chocolate chip cookie as an example. Quality could be defined as the degree of presence or absence of chocolate chips on the top of the cookie. The measurement of quality could be done through a vision system that counts the number of chocolate chips on the cookie and compares it to the total number of cookies that passed through the process. The quality is then calculated as the ratio of good cookies (those with chocolate chips) to the total number of cookies.
- Quality is slightly more complex, as it depends on what is deemed a quality product. However, once quality is defined, all that needs to be done is the measurement of this metric.
- Let’s say hypothetically that you are measuring if chocolate chips are in a cookie. If there is no presence of chocolate chips on the top of the cookie, it is a failure. To complete this, a basic vision system could identify the cookie, and then count the amount of chocolate chips seen.
- Once again, using a PLC or similar you would then measure the number of “good” cookies and divide it by the total amount that passed through
- To complete this you simply need the vision system to send the count of not only bad cookies but good ones too. You would then do some math to calculate good / (good + bad)
How to establish a baseline
Creating a baseline before making any process improvements is crucial for measuring the success of future automation and process improvements in the Industry 4.0 world.
One way to do this is by calculating the Overall Equipment Effectiveness (OEE) of an Industry 4.0 machine as it is currently. This provides a benchmark that can be used to compare future improvements against. It is important to continue revisiting this baseline over time, even after process improvements have been implemented. In some cases, process improvements may not lead to an improvement in the OEE, and it may be necessary to revert or iterate on the changes made.
By regularly monitoring the OEE, it is possible to identify any issues and make necessary adjustments to ensure that the machine is operating at its highest possible level of efficiency.
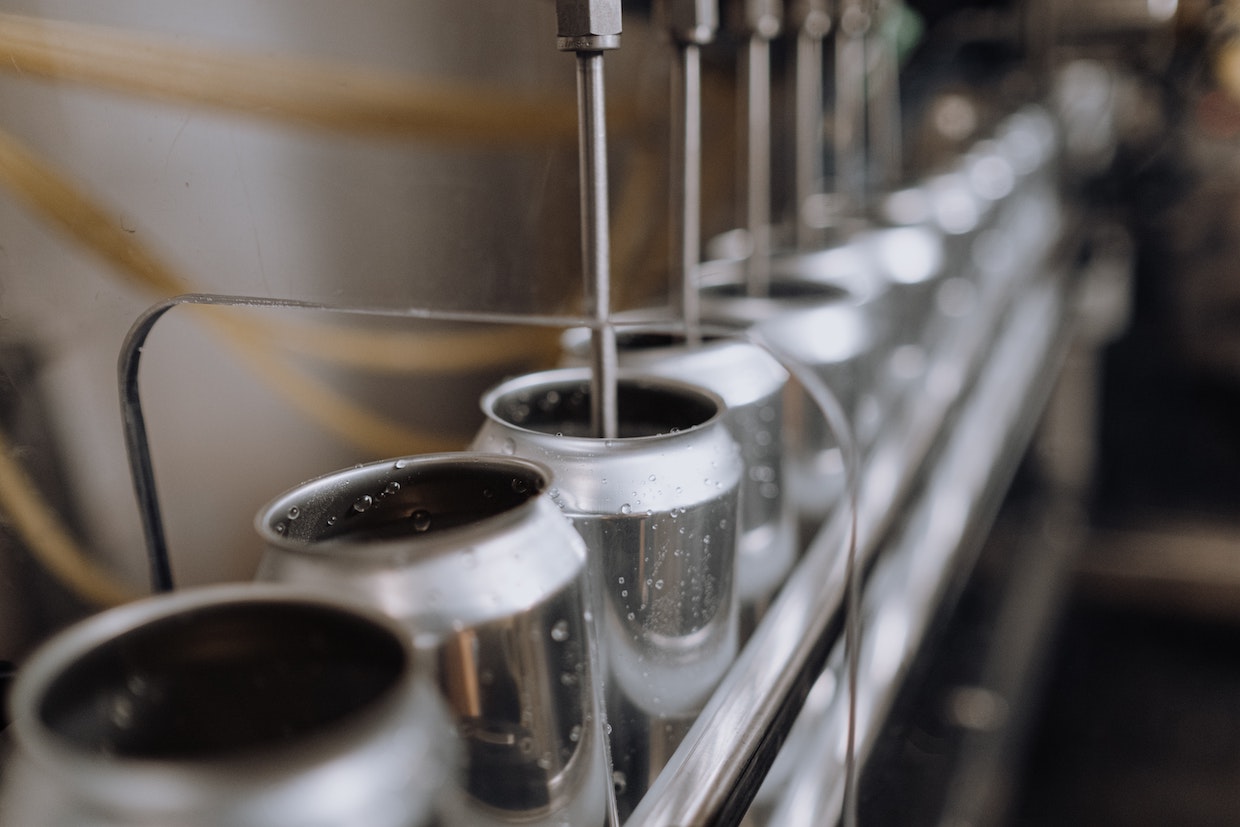
How to measure success
Measuring success in this context can be done by using OEE as the primary metric. OEE provides a comprehensive view of the process and allows for the calculation of overall efficiency.
One way to measure success is to estimate the Return on Investment (ROI) using multivariable methods, and then use OEE as a measure of success. By plotting the ROI and OEE over time, it is possible to see how the process has improved, and identify any areas that may need further attention. By comparing the OEE before and after process improvements, it is possible to determine the effectiveness of the changes made, and determine whether the investment in the improvements has been worthwhile.
By regularly monitoring and measuring success using OEE, it is possible to make data-driven decisions and continuously improve the process.
Creating a roadmap for future developments
Creating a roadmap for future development is an important step in achieving success within your processes and automation. While Industry 4.0 is built on top of creating efficiencies through technology, OEE allows you to be a bit more granular about the analysis. The production environments or similar are complex with many variables that represent system inputs and outputs, making solutions more complex.
However, OEE is still a valuable tool to quantify these environments. One consideration when creating a roadmap is that the return on investment (ROI) is compounded over time, and implementing solutions to individual problems may introduce too much risk to complete all at one time.
This requires a long-term approach to system improvements and dividing these projects into smaller chunks as defined within your roadmap. This allows for a more manageable approach to making improvements and reduces the risk of implementing changes that may not lead to success. By creating a roadmap, it is possible to plan for future development and make data-driven decisions that will lead to overall success for your business.
Conclusion
OEE is a powerful tool that provides a comprehensive view of a machine or process and its efficiency. The process of evaluating the overall automation can be boiled down to:
- Making the right thing – the right product or SKU (Stock Keeping Unit) at the right speed (Performance)
- Making it the right way – no rework, no defects, no waste (Quality)
- Making it at the right time – producing as planned, keeping the machine up and running, minimizing time losses (Availability)
OEE is a proven technique, with extensive resources available in the marketplace, and a useful methodology that can be applied to the smallest operation with manual data collection to the largest organization with sophisticated OEE software tools and SCADA systems.
Regardless of where you are within your digital transformation journey, Enginuity is here to help. Whether you are investigating it for the first time and need advice for data collection and implementation, or you are a multinational business with advanced software and integrations, we can help bring you to the next level.
Measuring these values is certainly step one, but you often need support to help offer the step change to the next level of efficiency.
How Enginuity uses OEE
Our Robotics and Automation team work closely with our electrical and mechanical engineers to develop robust and custom solutions for each client we engage with.
During our discovery process, OEE might be a part of the fact-finding process to determine where potential issues or problems exist.
We work with small and medium enterprises as well as large corporations across a wide range of industries including Aerospace and Defense, Industrial and Marine, Manufacturing, Product Development, Medical Devices, Food and Beverage, and more. Our cross-functional team has a wide range of expertise, ensuring that we get to the root cause of your problem while evaluating your long-term needs, so that you get the best service possible.
Is Enginuity the right partner for you? You can read about some of our past projects (and engineering case studies) and read why clients love working with us.
Our principles-based, agile engineering over the past 17 years is built upon our core mission of making a lasting impact to our clients and ensuring that they get what they truly need moving forward – no cookie-cutter engineering. No meaningless micromanagement. Just lean, fast, creative engineering leadership that understands and moves you forward to your goals, at your pace.
If you think we’ll be a good fit, we can start that conversation here.
Leave us your email and we’ll be in touch with you soon, along with instructions on how you can gain access to our LoRaWAN network.